北京培峰技术有限责任公司官方网站!
英文站
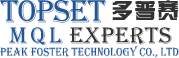
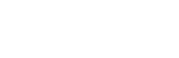
新闻中心
铝合金AA6061T6端面铣削中微量润滑的多目标优化
访问量:
11
本研究的目的是利用多目标遗传算法方法对AA6061T6端面铣削过程中的最小数量润滑(MQL)进行优化。采用响应面法和中心复合实验设计相结合的方法进行建模。从立式数控铣削中心采集数据,输入参数为切削速度、工作台进给率、切削轴向深度和最小润滑流量。在95%置信度水平上进行方差分析,以确定数控端面铣削过程中最重要的输入变量。采用多目标遗传算法对响应进行优化。利用多准则决策实用工具,在可行的优化设计范围内寻找操作参数和响应。采用迭代多准则决策算法,在多目标优化得到的多目标决策算法中,对给定条件进行了优化设计。在同等重量的情况下,得到的最佳设计是5252rpm的设计,进料速率为311mm/min,切割深度为3.47mm,MQL流量为0.44ml/min。
介绍
从成本、生态和人类健康问题以及加工工艺性能[1]的角度出发,微量润滑已被证明是一种有效的近干加工技术,也是一种完全干湿切削条件的有效替代方法。MQL是一种可持续的制造技术,对环境和工人都是安全的,具有成本效益[2-5]。切削液的成本在总加工成本的7%至17%之间,而另一项估计则将这一成本作为总加工成本的15-20%,而刀具成本在2%至4%之间[6-11]。因此,金属工质的最小化可以作为可持续制造的直接指标。MQL的目标是使用最小量的金属工作液(通常为50–500 ml/h)加工零件,其流量比洪水冷却条件下通常使用的量少约三到四个数量级[12-14],以便切割后工件、切屑和环境保持干燥。这个微量的概念,有时被称为近干润滑[15]或微润滑[16],十年前首次提出,作为解决润滑问题的一种手段与工厂车间空气中切削液颗粒有关的环境侵入和职业危害。在最近的过去,人们普遍倾向于干式加工[17]。另一方面,一些研究人员已经开始探索最小切削液的应用。与传统的湿法加工工艺和干法加工相比,最小润滑量提供了相当大的优势。被加工的零件用很小数量的流体喷在上面润滑,导致芯片、工具和工件上的润滑剂残留物非常低;因此,它们的清洗更容易和更便宜;芯片的回收很容易,因为加工过程的检查也很容易,因为加工区域没有被淹没。用MQL加工已广泛应用于钻孔[18-20]、铣削[21-26]、车削[19,27]和MQL磨削[28-31]等多种加工工艺]。MQL在机械加工的环境、工作条件和经济性方面对性能和质量有显著贡献。由于它不需要消耗电力的辅助设备,如压缩机、泵和冷冻机,就像在淹没润滑系统中使用的那样,它大大降低了能源消耗。除了环境和健康问题外,与切削液的应用、储存和处置有关的成本也是一个令人关切的问题。大约15%-20%的整体加工成本与冷却和润滑液[5,8,32]有关。到2007年,全球切削液的年消费量为6.4亿加仑[4]。考虑到与切削液相关的高成本和相关的职业接触,必须找到一种成本效益高的方法来制造产品。报道了MQL在钢加工中的应用[6,13,23,33-39]。这些研究的结果表明,MQL可以被认为是一种潜在的环境兼容以及经济润滑技术。以MQL为切削介质的加工研究主要集中在车削加工、钻削加工和磨削加工。在端面铣削[40]中使用MQL的文章很少发表。铣削过程中的通常做法是应用大量的液体冷却剂,随着间歇冷却的增加,液体冷却剂的温度变化[41]并积累边缘[42]。因此,简单地切断冷却剂的使用量不是端面铣削的实际答案,因为刀具尖端的切削作用是间歇性的,导致刀具尖端温度变化增加。因此,MQL作为一种潜在的方法的作用仍有待探索,以尽量减少热冲击在端面铣削中的后果,以消除在整个切削周期中产生的热量。
在[43]加工钢试件时,MQL有效地延长了刀具的寿命。然而,对铝合金[42]的加工还没有同样严格的研究。在文献中观察到关于合金冷却条件的相互矛盾的观点。由于切削温度[44]相对较低,通常认为在加工铝合金时不需要切削液。然而,由于铝合金具有较高的粘接特性[45],需要对其进行高效润滑。与钢和其他金属不同,切削液对于铝合金加工是必不可少的,以尽量减少对刀具边缘的涂抹效应,并降低表面粗糙度。与铝加工相关的技术问题还很少,如刀具磨损和机器可靠性等都需要解决。铝合金加工中的主要磨损机制是毛刺形成、堆积边缘和表面粗糙度。铝合金加工中的表面光洁度和毛刺形成主要用作刀具寿命标准,因为在铝合金加工中很难观察到刀具磨损[42]。然而,为了获得MQL的高冷却能力,必须选择具有高导热性的流体。冷却是加工工艺[46]中最重要的挑战之一。提高冷却速度的传统方法已经用尽到了极限[47]。鉴于上述在加工过程中提出的挑战,使用新的和创新的切削液是非常可取的,以实现高性能的冷却。与水浸和干加工相比,MQL是一种更实用的方法。使用MQL,当正确应用时,部件和芯片都保持干燥,更容易处理[48]。因此,它使金属芯片的回收更容易。MQL是一种以成果为导向的技术,它取代传统的润滑技术,接管润滑任务,以机械制造工艺协助可持续发展。大多数关于最小数量润滑和相关问题的研究都表明了MQL相对于使用常规乳化冷却剂的总体优势,并且在不同材料的加工中使用MQL进行了几次成功的实验。可持续加工的真正目标是使用最小数量的金属工质生产零件,使工件、切屑和环境在切割后保持干燥。为了实现这一目标,优化加工参数对有效使用昂贵的机床的加工性能具有重要意义。在大多数切削操作中,切削参数是根据手册推荐的操作范围设置的。其任务是为高效廉价的加工找到最佳的切削参数。许多研究都是为了优化加工参数而进行的,但其中大部分都是为了优化车削操作;然而,其他加工操作,包括铣削,[49]很少引起人们的兴趣。端铣是工业上应用最广泛的金属去除操作之一,因为它能够更快地去除材料,提供了相当好的表面光洁度[50]。由于铣削操作在当今制造业中发挥着重要作用,因此迫切需要优化这种操作的加工参数,特别是当使用数控机床时。加工工艺优化的意义源于加工工艺经济可行的前提条件。实际的制造过程通过相互冲突和往往不相容的性能度量来说明,例如质量和生产力[51]。采用多目标优化技术,找出加工过程中相互冲突的性能指标之间的权衡,以实现性能优化。在这种情况下,没有必要单一的解决办法能够满足所有的目标,因为这些目标之间的不协调和冲突。多目标优化不同于单一目标优化,因为单目标优化是用来从许多通常是最好的设计点中找到最佳设计的,是取决于优化[52]类型的全局最大值或最小值。本研究的目的是优化铝合金AA6061T6端面铣削中最小数量润滑的工艺。采用中心复合设计方法进行了实验。用最小润滑技术研究了在端面铣削中哪些参数是最重要和最有效的。采用遗传算法对端面铣削参数进行优化。遗传算法在优化加工参数特别是车削参数[49]方面是非常成功的。本文提出了一种基于多目标遗传算法的端铣作业约束优化问题。多目标优化问题通常有许多最优解,称为帕累托最优解[53]。该算法尝试的评估总数等于实验设计(DOE)表中的点数(初始总体)乘以世代数。将试样表面粗糙度、材料去除率和侧面磨损作为单道端面铣削约束参数优化问题的目标函数。一种商用无毒的微量润滑专用切削液(科特I或II)被使用。实验是根据微量润滑条件下的中心复合设计设计的。用周度计求平均表面粗糙度Ra。利用表面粗糙度和材料去除率的统计二次模型拟合表面粗糙度的实验数据。
方法论
加工参数与实验设计
本研究选择的加工参数为主轴转速,工作台进给量,切削深度和最小数量润滑剂流量。采用响应面法的中心复合设计方法进行实验设计,以求得到实验效果和参数组合。选取五个层次的加工变量,如表1所示。
表1。将加工参数进行分级。
参数的测量
本研究研究的响应变量为表面粗糙度,材料去除率和刀具侧面磨损。表面粗糙度和材料去除率是实验的两个相互矛盾的响应。表面粗糙度用周度计(MarSurfXR20(Mahr))测量,而材料去除率是通过每次切割后称重工件来计算的。表面粗糙度(Ra)以µm测量。用扫描电子显微镜测量侧翼磨损。
工件、刀具和切削液
试样工件材料为AA6061T6铝合金,以其良好的切削加工性和连续的切屑性,是工业上应用广泛的常用商业合金。工件尺寸100mm×100mm×30mm。实验中使用了同一批工件。Si、Cu和Mg是合金的主要成分。用于计算材料去除率的合金密度为2712kg/m3。选择了一种双槽无涂层碳化钨端磨机进行加工。实验采用中心复合设计方法设计,并应用二次响应面模型。进行优化,寻找最佳设计。方差分析(ANOVA)用于验证实验数据的充分性。 实验使用垂直数控铣削中心HAASVF6进行。试件上的毛坯和加工工件以及加工图案如图1所示。在机器上设置工件如图2所示。
图1。工件毛坯和已加工工件,尺寸为mm。
MQL系统
MQL通过系统传送到切割区。雾系统由用于空气和润滑剂混合的同轴喷嘴组成,保持恒定的雾化速率;通过计量泵的自动循环连续外部润滑,由空气压力和柔性喷嘴供电的可变速率脉冲发生器(4-200脉冲/分钟),提供定位的灵活性。脉冲发生器产生计量泵的重复循环。采用1滴计输出6喷嘴配置。系统设置6台正排量油计量泵(0.2-1.00毫升/冲程),行程可调,输出可调。采用空气计量泵控制气流进行雾化。MQL系统的不同组件如图3所示。通过将行程长度设置为10来调整MQL流量,而根据逆时针旋转来调整流量。
图2。工件的安装。
图3。MQL系统和设置。
结果与讨论
输入参数的意义
输入参数的意义是根据高、低水平两组实验设计的平均值的差异来确定的。通过使用DOE确定参数效应大小来评估主要参数的相对重要性和排名及其与响应变量的相互作用,如图4所示。总体饼图和表(图4表2)显示了每个输入变量相对于总体响应的贡献。从表面粗糙度的学生图可以看出,切割深度和工作台进给率是最重要的因素,而对于材料去除率来说,最重要的因素是切割深度。在侧翼磨损的情况下,进给率是最有效的参数。
图4。响应变量输入参数的意义。
表2。参数的意义。
采用多目标遗传算法模式II(MOGA-II)进行优化。实验的设计作为“初始种群”。初始种群由一组染色体组成。染色体在几次迭代中进化,称为世代[54]。最好的个体被评估,重组和突变,以构成一个新的种群。MOGA是第一代遗传算法[55],而MOGA-II是第二代进化算法。使用遗传算法进行优化的基本概念是,给定种群的遗传集合包含对给定问题的更好的解。在进化算法中应用的一般算子是选择、突变和交叉。MOGA-II算法实现了第四个算子。多搜索精英主义。选择操作员将设计转移到下一代,选择是基于功能的最佳适应度。具有更高适应度值的设计更有可能被复制到下一代中,以确保更适合的解决方案具有更高的生存概率。利用交叉和变异技术产生新一代。交叉分裂成两条染色体,然后将每条染色体的一半与另一对染色体结合。突变包括[54]翻转一个染色体。然后根据某些适应度标准对染色体进行评估,并保留最佳染色体,而其他染色体则被拒绝。精英算子能够保留所有非主导的解,而不回避初始种群,从而提高收敛速度。
采用遗传算法MOGA-II进行多目标优化。算法在100代后停止。从100代后得到的总可行解中选择帕累托解。帕累托优化方法的目的是确定一组参数,这些参数是设计的特征,超出这些参数,任何方面的性能都不能在不损害另一个方面的情况下得到改善。多目标优化的结果是一组主导其他设计的设计。这一组被称为帕累托最优集[56]。从数学的角度来看,从优化过程中得到的所有帕累托设计都被认为是同样可取的。这些设计数量庞大,因此,最终设计配置的选择对于实践是必不可少的。为了找出单一的最优解,采用基于MCDM技术的遗传算法,以帕累托前沿作为搜索空间,并将偏好权重分配给每个属性。在分配权重的基础上生成效用函数,并对所有帕累托设计进行排序。通过加权效用函数将多目标问题简化为单目标问题,满足设计-属性关系的所有偏好。MCDM方法包括属性设置、偏好权重分配、根据适应度评价标准对个体进行基于GA的排序。
目标职能
为了优化加工操作,需要定义一些目标函数。研究的优化问题是一个多目标优化问题。当使用最佳切削参数时,加工操作可以非常有效。在开始生产之前,需要确定最佳切割条件。进行优化,确定端面铣削工艺参数的最佳组合。本研究中用于优化加工工艺的自变量为切削的轴向深度、进给量、速度和最小数量润滑剂流量。在单通铣削参数优化问题中,采用评定轮廓的算术平均偏差、Ra、材料去除率和侧翼磨损作为目标函数。最小表面粗糙度不仅是质量指标,也是控制加工性能和运行成本[25]的最终阶段。表面粗糙度被测量为评估轮廓中所有测量值与该轮廓的平均线的算术平均偏差。标准长度(17毫米)的一段,根据可用的周度计的能力确定,从粗糙度图上的平均线取样。最大限度地提高材料去除率是作为优化基础的另一个目标函数。因此,这两个目标是相互矛盾的,即一个必须妥协,才能在另一个目标中取得收益。第三个目标函数是最小化侧翼磨损。
加工约束
除了目标函数外,加工操作也是由约束有效地定义的。这些约束是由过程能力和产品需求定义的。工艺能力包括实际的机器条件,允许的切削主轴转速,进给率,最大发热量和最大机器功率,而产品要求包括产品表面光洁度要求和所需材料去除率。为了执行有效的优化,这些约束必须完全满足。作为研究最优切削参数的解受一些边界条件的约束。在所提出的情况下,边界约束设置在实验范围内。
本研究中考虑的约束是由Eq给出的。(1)改为等式。(6)。
本研究采用多目标遗传算法(MOGA-II)策略对加工过程进行优化。遗传算法从一开始就被用于函数优化,以优化在许多科学和工程领域出现的、人们了解甚少的大型问题[57]。
帕累托设计
初级优化的结果是一组最优可行解,它显示了两个目标之间的权衡,称为帕累托集。帕累托最优设计的使用有几个优点。由于这些设计是从可行的设计中选择的,因此保证了优化设计的可行性。帕累托优化方法的目的是识别描述设计的一组参数,在此之后,任何性能方面都不能在不损害另一个方面的情况下得到改进。该方法提供了一种方法来理解设计器必须解决的冲突需求之间的权衡[28]。在目前的研究中,得到了52个帕累托设计。所有帕累托最优点的集合称为帕累托前沿。图4绘制了当前设计的帕累托前沿。
表3。最佳切削参数和响应变量。
优化结果
多目标优化的结果是从总共2600个设计中得到的一组1896个可行设计,其中39个设计属于帕累托前沿,即非支配帕累托最优解的集合。帕累托设计相对于输入设计变量的分布用气泡图表示。在气泡图中,x轴表示设计变量,而在y轴上表示一个响应变量,即。在这种情况下,表面粗糙度被绘制,而气泡直径和气泡颜色分别表示材料的去除率和侧面磨损。图5显示了帕累托最优设计相对于输入变量的分布。图5(A)显示了随着切割深度的增加,帕累托设计的分布。大多数帕累托设计位于整个切割深度范围内,最佳设计从0.5毫米到1.7毫米。对于进率,帕累托设计的分布(图5(B)显示,大多数设计是在280毫米/分钟到300毫米/分钟之间获得的。一些表面粗糙度和侧面磨损较低的设计也发现了较高的进给率。几乎所有的帕累托设计都是以最小速度找到的,如图5(C)所示)。最可行的帕累托设计是在0.77毫升/分钟到0.80毫升/分钟的MQL流量范围内得到的,如图5(D)所示)。为了在位于帕累托边界的解决方案中选择一个最优的折衷方案,采用多准则决策技术。根据响应变量之间的非偏好关系,所有的解都被分类为秩值。表3给出了初始解和最优解在自变量、目标参数和约束方面的比较。常规MQL中未涂覆碳化钨插入件的表面粗糙度比初始最小值高25.7%,但表面粗糙度值仍低于最高值74.2%。侧翼磨损的最小值增加了1.0%,而最大侧翼磨损值则提高了58.4。材料去除率的最优值相对于最小测量值要高得多。
图5。气泡图显示帕累托设计分布相对于输入参数。
结论
在上述研究中,采用遗传算法对具有最小润滑量的数控铣削操作进行了多目标优化。刀具的表面粗糙度、材料去除率和侧面磨损是有待优化的相互矛盾的响应。从可行的设计中,选择帕累托设计进行进一步的研究。针对帕累托设计,提出了一种多准则决策算法。这些设计是根据它们的适合度来进行最优标准的排序的。给出了三个目标函数的等权重,得到了优化设计。在同等重量的情况下,得到的最佳设计是5252rpm的设计,进料速率为311mm/min,切割深度为3.47mm,MQL流量为0.44ml/min。表面粗糙度的最佳值为0.543µm;材料去除率为15173mm3/min,优化后的侧翼磨损为15.95µm。由此获得的一系列可行的实验设计以及选定的优化设计可以作为定义域内制造实践的未来基准。